The Production Process Of Snowtubes Generally Includes The Following Key Steps:
Tháng 12 23, 2024
1. Raw material preparation: Select suitable plastic particles, such as high-density polyethylene (HDPE), etc. These raw materials must have good cold resistance, wear resistance and impact resistance to ensure that the Snowtube as PVC snow tube can maintain stable performance in low temperature and frequent use environments. Put the raw materials into the drying equipment for full drying treatment to remove the moisture in them, so as to prevent bubbles or defects caused by water vapor in the subsequent processing process, which will affect the product quality.
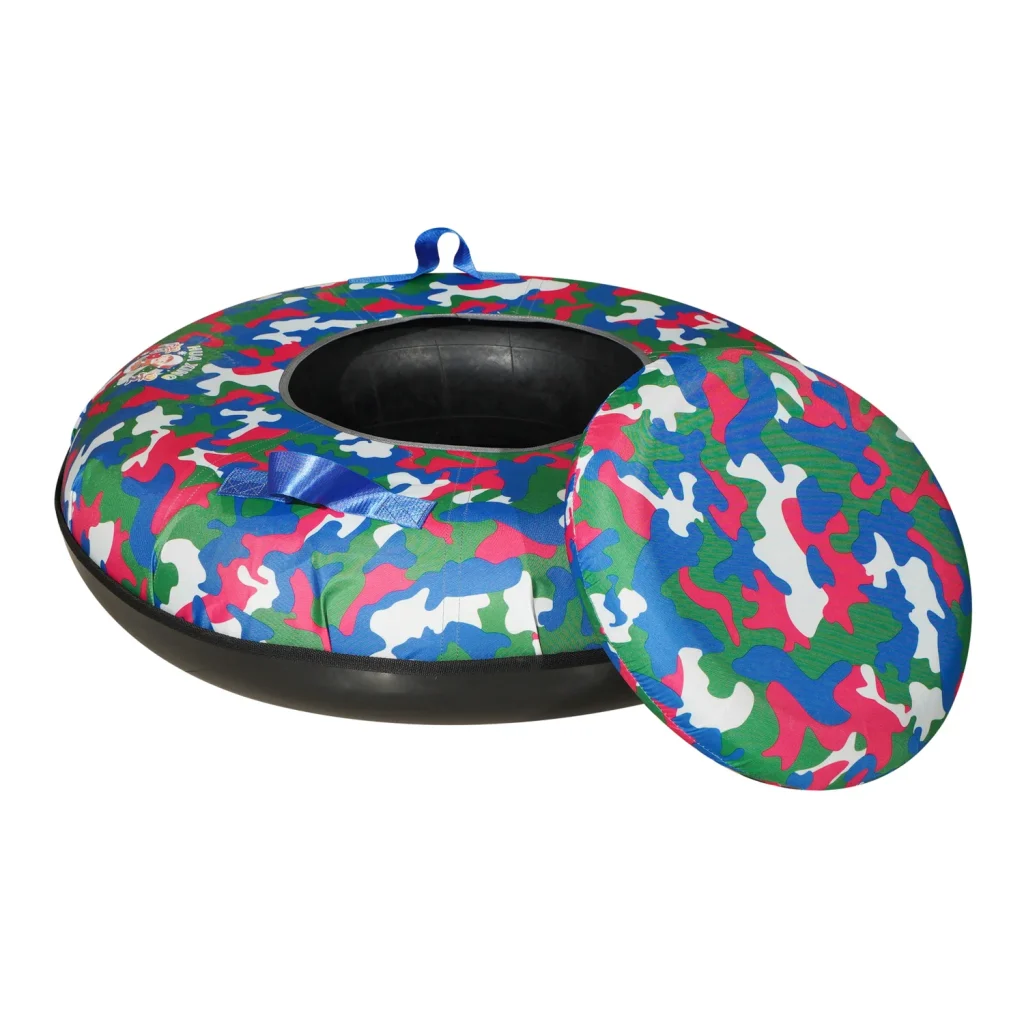
2. Injection molding: Add the dried plastic raw materials to the hopper of the injection molding machine, and the injection molding machine heats the raw materials to a molten state. Subsequently, under high pressure, the molten plastic is injected into the specific Snow tube mold cavity. The design of the mold cavity determines the shape, size and surface texture of the Snowtube. During the injection molding process, parameters such as temperature, pressure and injection speed must be accurately controlled to ensure that the plastic fills the mold evenly and forms a complete and defect-free Snowtube blank. For example, too high a temperature may cause plastic degradation, while too low a temperature will make the fluidity worse and affect the molding effect; insufficient pressure is prone to material shortage, and excessive pressure may cause overflow or mold damage.
3. Cooling and shaping: The temperature of the newly injection-molded Snowtube is high and the texture is soft, so it needs to be cooled and shaped in the mold. The heat of the Snowtube can be quickly removed through a circulating cooling water system or other cooling methods, so that it gradually hardens and reaches a stable shape and size. The length of the cooling time will affect the production efficiency and product quality. If the cooling time is too short, the Snowtube may be deformed due to the incomplete solidification of the internal structure; if the cooling time is too long, the production efficiency will be reduced and the production cost will be increased.
4. Demolding and trimming: After the Snowtube is cooled to a certain degree, open the mold and use the demolding mechanism to remove it from the mold. The Snowtube after demolding may have some defects such as flash, burrs or gate residues, which need to be trimmed. Usually, trimming tools or grinding equipment are used to remove the excess parts to make the surface of the Snowtube smooth and flat, meeting the product appearance requirements.
5. Quality inspection: Perform a comprehensive quality inspection on the trimmed Snowtube. Including appearance inspection to check whether there are surface defects, uneven colors, etc.; size measurement to ensure that the key dimensions of the Snowtube, such as diameter and thickness, meet the design standards; performance testing, such as impact resistance testing, simulating the collision that the Snowtube may be subjected to during use, and testing whether it can withstand the corresponding impact force without breaking or being damaged. Only Snowtubes that pass strict quality inspections can enter the subsequent packaging stage.
6. Packaging and warehousing: Qualified Snowtubes are packaged according to the specified quantity. Generally, plastic film, cartons or woven bags are used as packaging materials. During the packaging process, attention should be paid to protecting the Snowtubes to avoid scratches, squeezing and other damage during transportation and storage. The packaged Snowtubes are transported to the warehouse for storage, waiting for shipment and sale.